在技术中心有这样一组专属数字,“14213”。这组数字概括了公司推行研发设计工艺一体化以来取得的一系列成绩,也是打造太重标准、提升太重质量、树立太重品牌的一组密码——截至目前,中心总体设计改进106项,批量产品累计制造49台,单件小批量产品研发设计27台,配套零部件产品工艺优化12项,铸锻件产品制造完成370吨。
今年,公司科技质量大会和公司党委中心组(扩大)专题学习会多次强调,要按照研发设计工艺一体化、制造采购安调一体化、工艺质量检验一体化管理思路,推动产品设计、营销、管理标准化、系列化、模块化、平台化。
按照公司《研发设计工艺一体化工作方案》要求,技术中心全面推进研发设计与工艺的相互融合,以全方位服务生产制造需求为主线,根据批量型、单件小批量、配套零部件和铸锻件四种不同类型产品的设计制造特点,制定了四类不同产品实施计划,明确时间表、责任人、路线图,工艺设计、研发制造成果显著。
研发设计
以服务生产产线和生产工序为主线,技术中心按产线工位需求,共进行了106项精细化设计,如优化图纸层级、补充工艺信息、固化电气及液压管路走线、装夹定位工装等。不仅畅通了生产流程,还实现了降本增效。
批量化产品

技术中心从设计源头进行研发设计工艺一体化规划,在宽体车、叉车、剪叉式高空作业平台等批量化产品上稳步推进,结合产线工艺流程、产品特点和工位布局,围绕图纸层级优化、模块化设计、工艺信息上图纸、管路布局优化等方面展开工作,生产效率明显提升,产品质量有效改善,制造成本持续降低,批量化产品的核心竞争力大大增强。当前,共49台批量化产品制造完成。
单件小批量产品
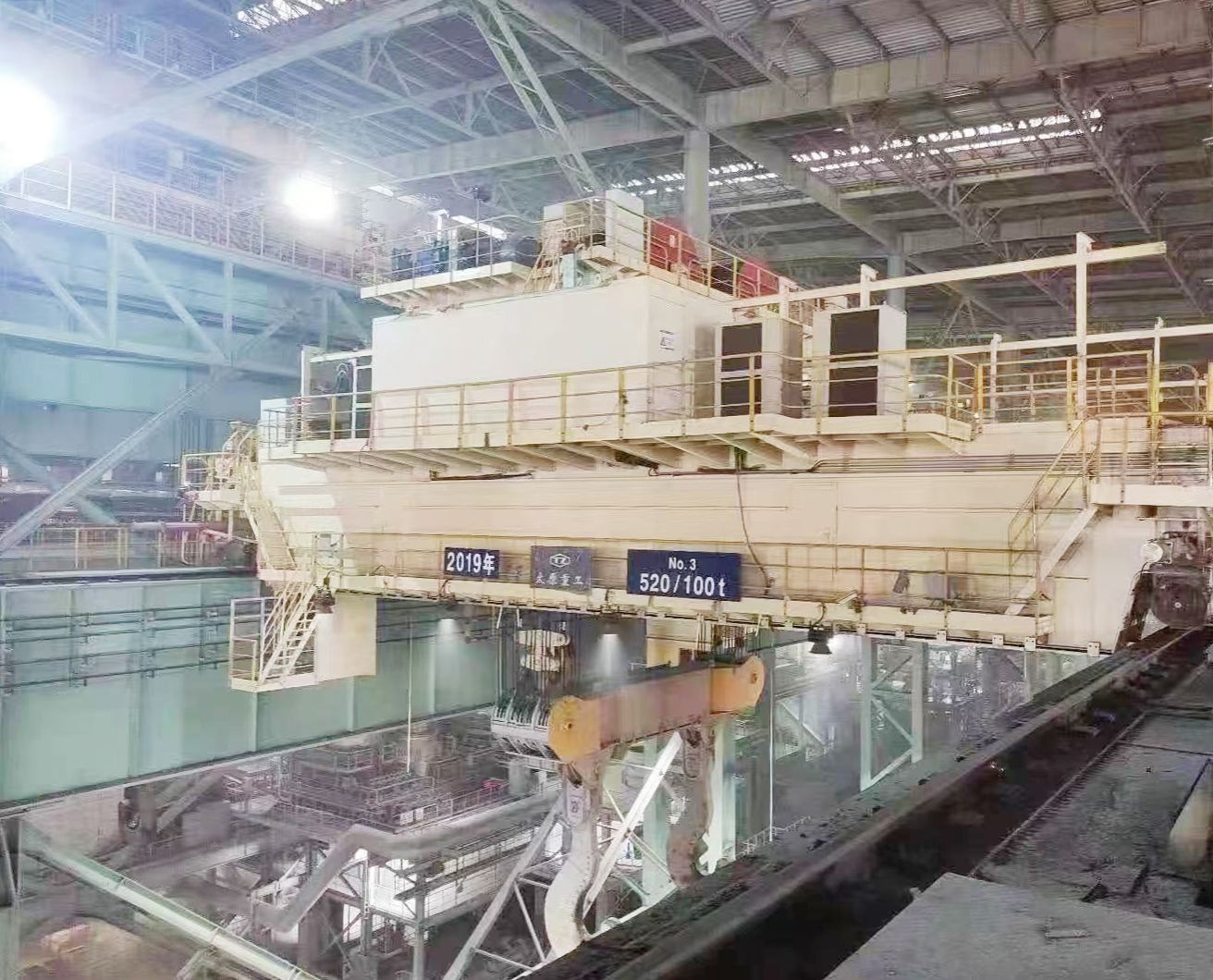
围绕生产服务、精细设计和降本增效等方面,技术中心积极推进研发设计工艺一体化工作。以起重机产品为例,面对主梁超长板对接拼焊不规范的问题,设计人员结合公司采购标准板材规格,制定了起重机主梁板材拼接规范,从设计端明确标注超长板的焊缝位置和焊缝形式,提高了板材利用率,保证了主梁焊接质量。三个月时间,包括起重机、矫直机在内,共27台单件小批量产品完成研发设计改进工作。
配套零部件产品
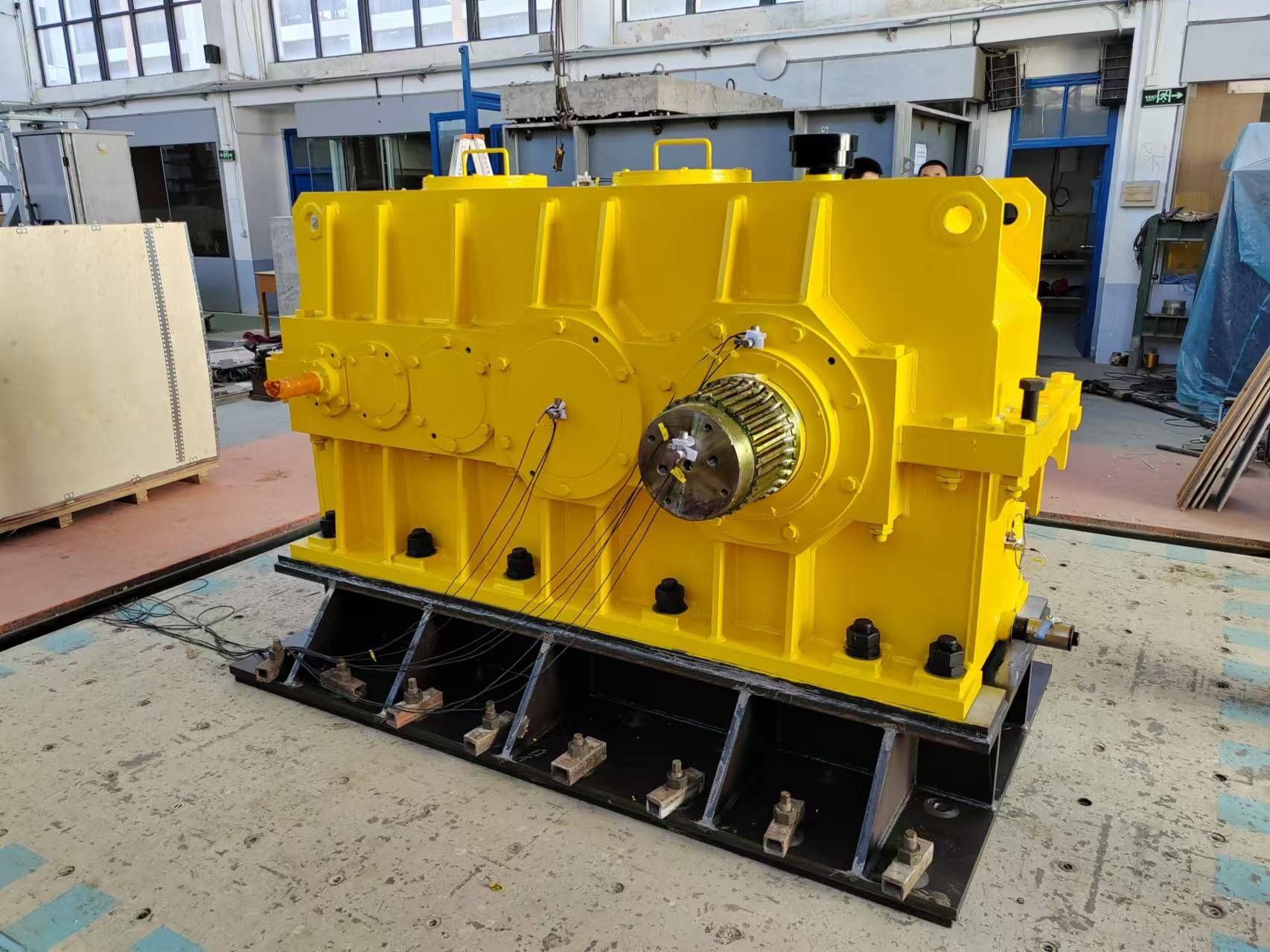
配套零部件直接影响着整机设备的质量和性能。在配套零部件产品改进方面,技术中心齿传专业选取公司重点产品配套减速机作为试点,以问题为导向,提出解决措施,先后开展了螺栓力矩标注、增加产品结构改进、模块化设计等12项工艺融合工作,齿轮箱产品质量明显改善。
铸锻件产品
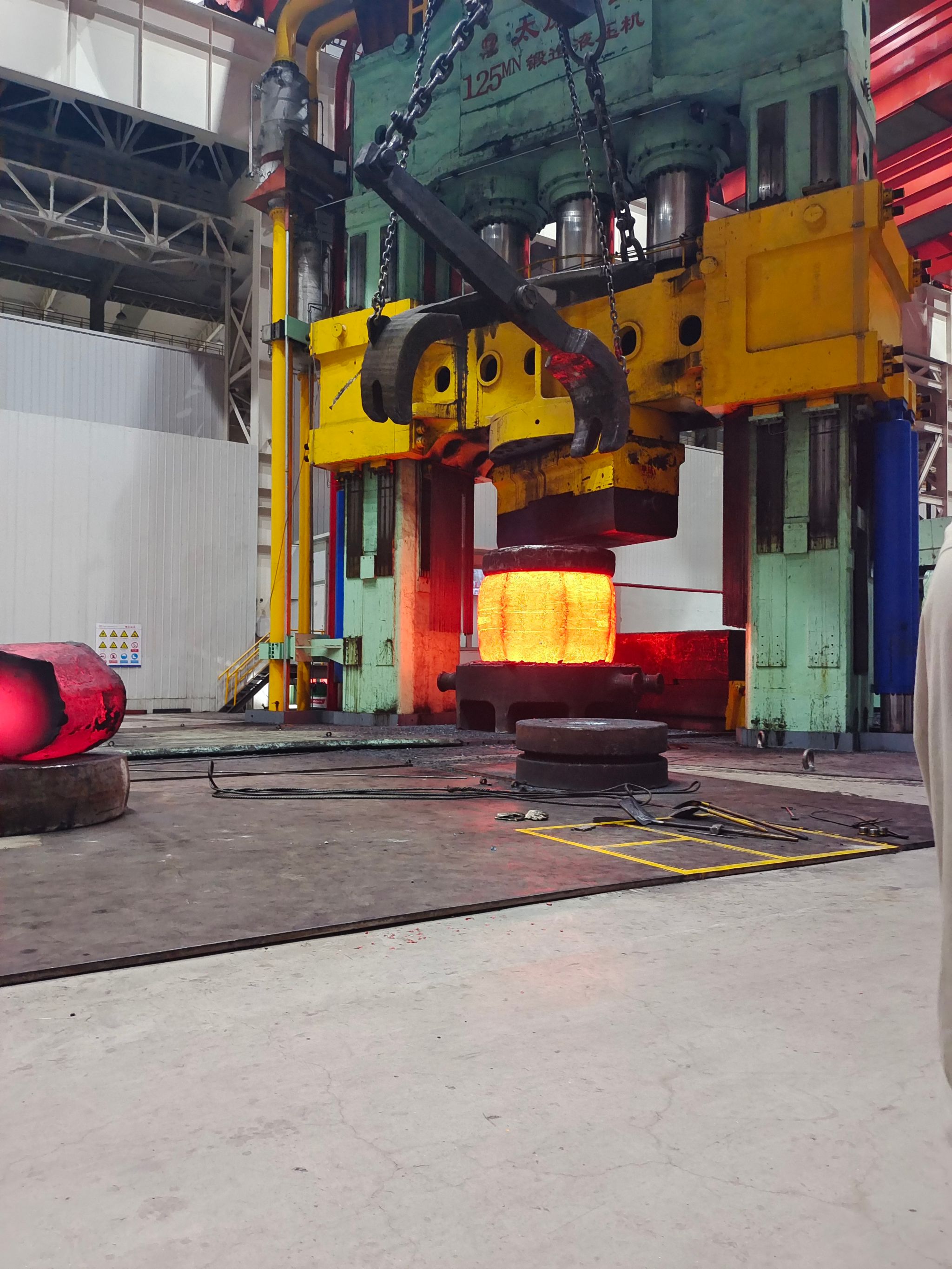
技术中心热工所在模具钢的开发制造过程中,从材料成分优化、锻造工艺和热处理等方面入手,验证铸锻件产品研发设计工艺一体化工作思路和方法,建立规范化设计体系,实现了质量、效率和成本控制的全面提升。截至目前,370吨铸锻件产品制造完成。
在围绕具体产品开展工作的同时,技术中心还注重技术人员的能力培养和提升,针对性地制定年度培训计划,要求工艺技术专家对设计人员进行焊接、机加工、装配、工艺装备等工艺基础知识培训,现已累计开展培训106课时。通过工艺培训,增强了设计人员对生产装备和制造工艺的全面了解,将工艺知识陆续运用到产品设计中,从而对设计工艺融合有了更加深刻的认识,产品设计的精细化水平明显提高。
未来,技术中心将认真总结经验做法,继续巩固和扩大工作成果,以点带面形成辐射引领,彻底打破设计工艺壁垒,全面提升产品质量、生产效率和成本管控水平,为把太重真正打造成为跨越时空、基业长青、朝气蓬勃的百年老店贡献技术力量!